In an industry where resistance and performance are paramount, the choice of materials plays a crucial role. Whether ensuring perfect sealing or optimizing forming processes, elastomers offer indispensable technical advantages.
Optimize elastoforming with polyurethane
Elastoforming is an essential process for metal part stamping in the aerospace industry. Its efficiency relies on the use of polyurethane pads, which conform to the shape of a punch to shape metal sheets with exceptional precision. However, the durability of these pads poses a significant challenge: premature wear leads to production interuptions and considerable replacement costs.
Designed to meet the most stringent requirements across numerous industries, our UREFLEX® polyurethane range stands out due to its unique mechanical properties. Their high resistance to tearing and wear allows them to withstand repeated stresses without early degradation. This extends the lifespan of the pads and reduces maintenance needs. Their excellent elongation capacity ensures optimal flexibility to accommodate metal deformation, while their low compression set guarantees a return to their original shape after each cycle, maintaining long-term efficiency.
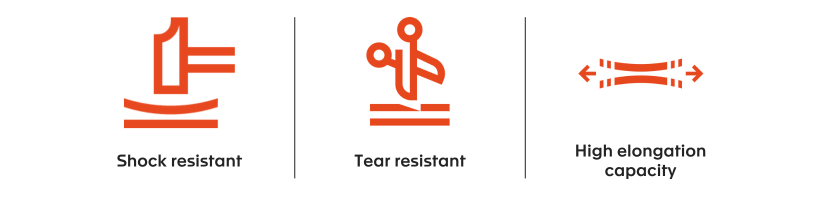
Thanks to their unique properties, UREFLEX® polyurethanes offer the most reliable and high-performance alternative to traditional materials used in elastoforming. They deliver consistent and precise metal shaping while minimizing tooling stress, directly enhancing the profitability of manufacturing processes.
Inflatable silicone seals: the sealing solution
A dynamic solution for sealing and protection challenges
In aerospace applications, pressurized environments, extreme thermal variations, and mechanical stress demand high-performance sealing systems.
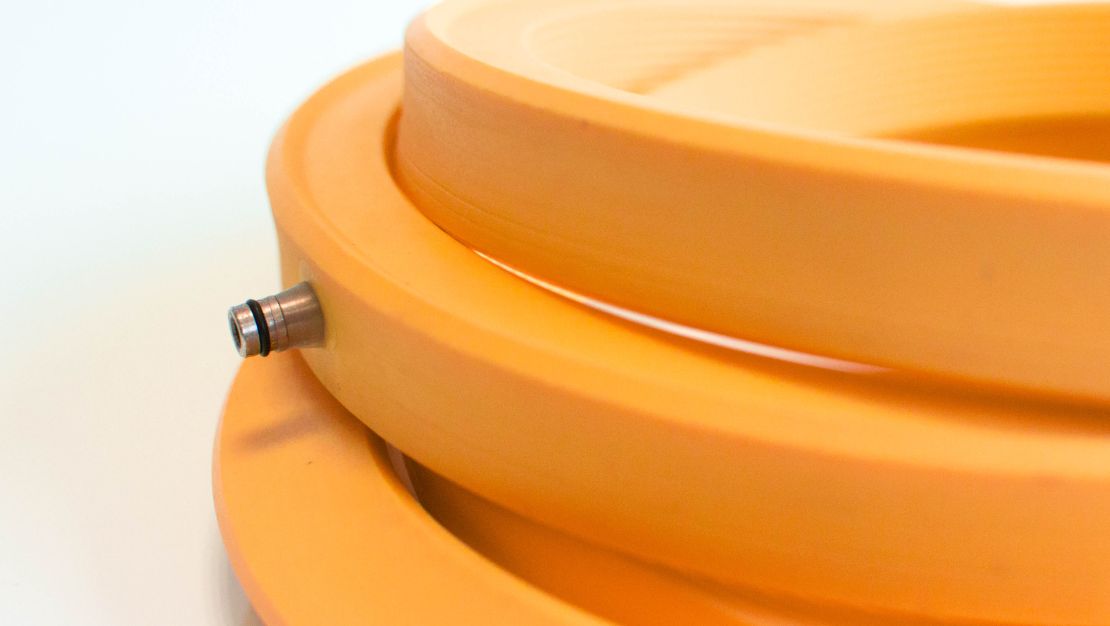
The silicone inflatable seal stands out as a smart technological solution: when pressurized with air or gas, its hollow profile expands to exert uniform force on the surfaces to be sealed—whether curved, irregular, or mobile—ensuring reliable sealing performance. It also serves as an effective alternative for holding components in place, acting as an atraumatic device for pressing, gripping, or handling during assembly or maintenance operations.
High-performance technical materials
Our silicone inflatable seals are extruded and vulcanized from High Consistency Rubber (HCR) elastomers. Designed to meet the demanding standards of the aerospace industry, their technical properties—such as flame resistance, low smoke emission, chemical compatibility, and the ability to withstand temperatures from -60°C to +300°C—open the door to a wide range of applications.
Our expertise, your performance
- Custom design: Our R&D team considers your dimensional, regulatory, and lifecycle requirements to define the ideal seal profile (axial or radial).
- Multi-continental industrial capability: Production sites in France, Italy, and Brazil secure your supply chain and reduce time-to-market.
- Quality control: Dedicated test benches for inflatable seals ensure full compliance and reliability.
Our silicone product ranges
- Diodon™: High-performance inflatable seals
- Hightube®: For tube connections, fittings, and weld joints